GENERAL CHEMICAL RESISTANCE OF VARIOUS
ELASTOMERS The following pages
are offered as a general guide to the suitability of various elastomers in
use today for service in these chemicals and fluids.
The criteria used for the ratings were primarily volume swell resistance,
compression set resistance, and aging resistance. For the most part the
ratings were arrived at from specific data or general agreement of the
sources named below. In circumstances when no data or agreement was found,
the ratings were arrived at by theory and analogy. In some cases, they are
the considered opinion of experienced compounders. We cannot guarantee their
accuracy nor assume responsibility for their use. Several factors must
always be considered in using a rubber part in service. The most important
as we see them are:
A. The Temperature of Service: Higher temperatures increase the effect of
all chemicals on polymers. The increase varies with the polymer and the
chemical. A compound quite suitable at room temperature might fail miserably
at elevated temperature.
B. Conditions of Service: A compound that swells badly might still function
well as a static seal yet fail in any dynamic applications.
C. The Grade of the Polymer: Many types of polymers are available in
different grades that vary greatly in chemical resistance.
D. The Compound Itself: A Compound designed for other outstanding properties
may be poorer in performance in a chemical than one designed especially for
fluid resistance.
STANDARD DIMENSIONAL TOLERANCE TABLE-----------MOLDED RUBBER PARTS
Metric Size(MM) |
A1 |
A2 |
A3 |
A4 |
Above |
Include |
Fixed
+/- |
Closure
+/- |
Fixed
+/- |
Closure
+/- |
Fixed
+/- |
Closure
+/- |
Fixed
& Closure
+/- |
0 |
4.0 |
0.08 |
0.10 |
0.10 |
0.15 |
0.25 |
0.40 |
0.50 |
4.0 |
6.3 |
0.10 |
0.12 |
0.15 |
0.20 |
0.25 |
0.40 |
0.50 |
6.3 |
10 |
0.10 |
0.15 |
0.20 |
0.20 |
0.35 |
0.50 |
0.70 |
10 |
16 |
0.15 |
0.20 |
0.20 |
0.25 |
0.40 |
0.60 |
0.80 |
16 |
25 |
0.20 |
0.20 |
0.25 |
0.35 |
0.50 |
0.80 |
1.00 |
25 |
40 |
0.20 |
0.25 |
0.35 |
0.40 |
0.60 |
1.00 |
1.30 |
40 |
63 |
0.25 |
0.35 |
0.40 |
0.50 |
0.80 |
1.30 |
1.60 |
63 |
100 |
0.35 |
0.40 |
0.50 |
0.70 |
1.00 |
1.60 |
2.00 |
100 |
160 |
0.40 |
0.50 |
0.70 |
0.80 |
1.30 |
2.00 |
2.50 |
160 & over |
0.3% |
0.4% |
0.5% |
0.7% |
0.8% |
1.3% |
1.3% |
|
Remark: |
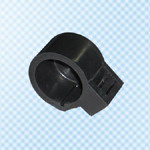 |
a) A1 grade for precision molded
rubber |
b) A2 grade for
excellent quality molded rubber |
c) A3 grade for good quality
molded rubber |
d) A4 grade for
suitable quality molded rubber |
e) F stand for regular size
which will change when mold move. |
f ) C stand for width size which
don't change when mold move. |
g) Drawing
designation "A2" tolerances indicate a precision product. Molds
must be precision machined and kept in good repair. While
measurement methods may be simpler than with Drawing Designation
"A1", careful inspection will be required. |
ASTM2OOO & SAE J200
Classifications System for Elastomeric Materials for Automotive Applications
This specification system has been devised jointly by the ASTM Committee D
11 on rubber and rubberlike material and the Society of Automotive Engineers
(SAE). It is of sufficient interest and importance to warrens its
reproduction in part and to show how it may be used. The following may be
considered an abbreviated course on how to interpret a typical "line
call-out" or specification using the example outlined in the D 2000
publication.
An example line call-out may comprise the following letters and numbers:
2BC 510A14E034
The first portion of the call-out is called the basic requirements. This
consists of the 2BC 510. The basic requirements may be interpreted as
follows:
2 = Grade number. This defines the performance level for she suffix
requirements.
B = The material type. This defines the aging temperature requirements. B
type materials are aged at 100°C (212° F)
C = The material class. This determines the oil swell requirements. C class
materials have a 120% maximum volume swell in ASTM No. 3 Oil.
5 = The target hardness, 50 + 5 Shore A
10 = The minimum tensile strength, 1000 psi. If the line call-out starts
with the letter M (for metric), the tensile is given in MPa (Since 1000 psi
= 7 MPa, the equivalent metric call-out is M2BC 507.)
The letters and numbers following the basic requirements are called the
suffix requirements. These are added only as needed to meet specific end-use
requirements. For example, the A14E034 suffix requirements may be
interpreted as follows:
A = Special heat resistance, -15% maximum tensile change and -40% maximum
elongation change. Without the A14 suffix, the basic type materials are
permitted + 30% tensile change and -5% elongation change after heat aging.
1 = The test method for heat resistance, ASTM D 573 for 70 hours.
4 = The test temperature for heat resistance, 100°C (212°F).
EO = Fluid resistance (oils end lubricants). As the case for heat
resistance, this suffix allows less change in properties after ASTM No. 3
Oil immersion than the basic C class material.
3 = The test method for fluid resistance, ASTM D 471 in No. 3 Oil for 70
hours.
4 = The test temperature for heat resistance, 100° C (212° F).
| ELASTOMER
COMPOUND SELECTION
Many different compounds are needed to meet the wide range of service
conditions found in the oilfield and industrial markets. A broad range
of elastomers to choose from is essential. The list below shows some of
the common oilfield elastomers and their general properties. |
|
|
|
|
|
|
|
|
|
|
High Temperature |
250°F |
300°F |
400°F |
450°F |
450°F |
300°F |
600°F |
450°F |
Low Temperature |
-40°F |
-40°F |
-20°F |
-20°F |
0°F |
-60°F |
-80°F |
-80°F |
Acid Resistance |
3 |
2 |
1 |
1 |
1 |
2 |
3-2 |
3-2 |
Base Resistance |
3-2 |
2 |
4 |
2 |
1 |
1 |
3-2 |
3 |
Oil & Fuel
Resistance |
1 |
1 |
1 |
1 |
2 |
4 |
4 |
2 |
Water & Steam |
3-2 |
2 |
3-2 |
2 |
1 |
1 |
3 |
3 |
Gas Impermeability |
2 |
2 |
2 |
2 |
2 |
2 |
4 |
4 |
Ozone Resistance |
4 |
2 |
1 |
1 |
1 |
1 |
1 |
1 |
Compression Set |
2-1 |
2-1 |
2-1 |
2-1 |
3 |
2-1 |
2-1 |
2-1 |
Abrasion Resistance |
2 |
1 |
2 |
2 |
5 |
2-1 |
6 |
6 |
Resilience |
3-2 |
2 |
3 |
5 |
4 |
2 |
2 |
2 |
Tear Strength |
3-2 |
2 |
3 |
3 |
2 |
2-1 |
4 |
4 |
|
|
NBR
COMMON NAMES: Nitrile, BUNA, BUNA-N
DESCRIPTION
Nitrile is the most widely used elastomer in the oilfield because of
it's low cost, good temperature resistance and strong resistance to oil
and petroleum based products.
APPLICATIONS
NBR works well in water, petroleum oils and fuels, ethylene glycol and
silicones but is not recommended for use in strong acids, bases, ketones,
phosphate ester hydraulic fluid, and halogen derivitives.
HNBR
COMMON NAMES: Hydrogenated Nitrile, HSN, Highly Saturated Nitrile
DESCRIPTION
The unsaturated double bonds within a nitrile's butadiene segments are
the main attack sites for heat, chemicals, and oxidation. The
hydrogenation process reduces the unstable double bonds between carbon
atoms in the polymer chain, allowing saturation rates of 85% to 99.9%.
The result is a high perfomance polymer with improved chemical and
temperature resistance.
APPLICATIONS
HNBR will have better resistance to acids, bases, heat, ozone, and
abrasion than NBR. It is a good choice when standard NBR compounds are
being pushed to their limits. HNBR is not recommended for service in
hydrocarbons (chlorinated), ketones, esters and ethers.
FKM
COMMON NAMES: VITON®, Fluorocarbon, fluoroelastomer, FPM
DESCRIPTION
FKM contains flourine atoms and is commonly referred to as a
fluorocarbon elastomers. The flourine atom to carbon atom bond is
extremely strong, and make FKM compounds extremely stable. The polymer
chain is also fully saturated, containing no unstable double bonds
between carbon atoms. Fluorocarbons have exceptional resistance to
chemicals, oil, ozone, and high temperatures.
APPLICATIONS
Highly resistant to the H2S and CH4 found in extreme service wells,
acids, aromatic hydrocarbons, solvents, and silicone fluids and greases.
FKM is not recommended for service in ketones, amines, low molecular
weight esters and ethers, and steam. | |
It is updating... |
| |
Back Home
Copyright© 2003-2010, Ningbo Yaseki Plastic and Rubber
Co., Ltd. All rights reserved.
Site Map |
|